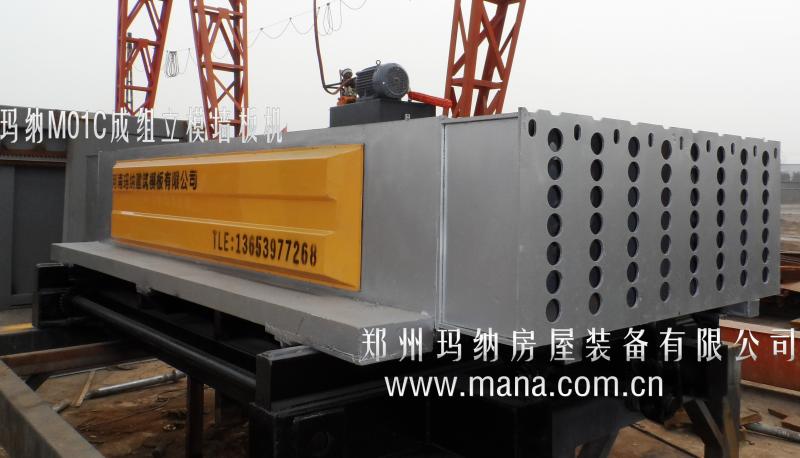
M01C型成组立模墙板机
墙改二十年成绩斐然,主要墙体材料之一的块状墙体材料如:各种砌块、各种非粘土砖、各种空心砖等,得到了广泛应用,其产品品种、产品质量、产品规模、装备水平及市场环境等都已达到了空前高的水平。
而作为另一类主要墙体材料的墙板,其应用与发展和块状墙体材料相比,则相对滞后。
随着劳动力价格的提高、生产效率期望的提高、建筑质量的提高、房屋抗震等级的提高、高层建筑比例的提高以及住宅产业化水平的大幅提高,市场对墙板研究、应用、生产制造的重视程度日趋强烈,同时,对墙板主要生产装备之一的——“成组立模墙板生产线”的关注度也急剧提高。
从本期开始,我们将对成组立模装备及其生产工艺的发展历程、技术内涵、前景展望作出系统介绍,欢迎参与。
成组立模工艺与平模工艺、挤出工艺统称为墙板生产三大主要工艺。
一、成组立模工艺与其它工艺相比,具备以下明显特点:
1、成型精度高。成组立模采用的是模腔双面成型原理,所以,生产的墙板几何精度,尤其是表面平整度和厚度精度是其他工艺所无法比拟的。墙板安装后,直接批档即可,无需抹灰。墙板高精度的直接结果是节材节能,节约劳动力成本,综合效率高,综合成本低。
2、成型墙板材料的灵活性。立模的模腔成型方式,使其对成型墙板材料的使用范围极其宽泛,所以无论是水泥基、石膏基、菱镁基等材料均可使用,且对材料的流动度、塌落度并不敏感,故工艺性好,便于质量控制和工业化生产。
3、成型墙板结构形式的广泛适应性。由于墙板技术要求的不同,使用范围的不同,服务对象的不同,其结构构造形式差别较大:如外墙板、内墙板;匀质板、复合夹芯板;圆孔板、方孔板;承重板、非承重板等,其断面形式与建筑物结构主体的联接方式均不相同,而立模工艺则可方便的满足不同墙板的不同需求。
4、结构紧凑,节省空间,节约资源。成组立模的成型模腔由于采用了直立的集约式安装形式,所以单位面积的有效生产效率高,因此占地面积小,节省空间。与其它工艺相比,可节约车间使用面积50%——80%,故特别适宜中小企业灵活创业,更适合大企业的大规模室内生产。
二、成组立模的优势领域
成组立模是一种个性鲜明的工艺装备。
成组立模灵活程度不如平模。平模可以自由的拼装,方便的改变成型形状,低成本的生产出各类异型墙板。而成组立模则更适合于规模化生产相对标准化的高品质产品。
成组立模生产的流畅性不如挤出式设备。挤出机属于连续流水生产,而成组立模则属于周期性的循环式生产。但成组立模可生产的墙板类型十分丰富,如加筋墙板、加网墙板、加网架墙板、布置预埋件墙板、夹芯复合墙板等。
成组立模对以下三类产品有着明显可见的可比优势。
(一)复合夹芯板类墙板:
1999年5月,在国家建材局组织的“玛纳机动成组立模”技术成果鉴定会上陈福广教授及其精辟的指出,基于成组立模的工艺特点,它最明显的优势是对复合夹芯板的生产。
面前,国内墙板市场上生产产量最大、占据主导地位的是轻质圆孔内隔墙板。随着建筑节能标准的提高,低碳经济的深入人心,复合夹芯板迎来了极好的发展机遇。
所谓“复合”,是当今极富时代特征的一种思维模式,“复合”即优势集合,如“复合型人才”、“复合型城市”、各类“复合”材料、塑钢复合门窗、铝塑复合管等等。
对于墙板而言,也是如此。任何一种材料,不可能具有你所需要的所有优势,如外墙板所需要的物理力学性能指标、物理热工性能指标、化学的耐久性、稳定性、防火性指标等,要想达到你所需要的优异性能,只有通过把各种功能材料复合在一起,才能把各种优点集中在一起,才能满足你的要求。
复合夹芯板有四类九种。
1、成型面板、浇注芯板类:
(1)纤维水泥面板(硅钙板)浇注聚苯球水泥夹芯复合板;
(2)纤维水泥面板(硅钙板)浇注泡沫水泥夹芯复合板;
(3)纤维水泥面板(硅钙板)浇注泡沫石膏夹芯复合板;
2、成型芯板、浇注面板类:
(4)钢筋网架聚苯夹芯浇注水泥面层复合板;
(5)钢筋网架彩钢聚苯夹芯浇注水泥面层复合板;
3、面板、芯板先后成型可选择类:
(6)水泥浇注面板、钢筋网架、泡沫水泥浇注芯板复合板
(7)水泥浇注面板、钢筋网架、泡沫石膏浇注芯板复合板
(8)水泥浇注面板、钢筋网架、泡沫轻骨料料浆浇注芯板复合板
4、立模挤压式薄抹灰成型类:
(9)立模挤压式薄抹灰聚苯夹芯保温板。
复合夹芯板的工艺特点是:
1、成型面板、浇注芯板类:首先将水泥纤维面板植入立模模腔,紧贴腔壁,有效定位(这些应由面板植入定位机构完成),然后浇注芯料料浆。
2、成型芯板、浇注面板类:首先将钢筋(钢丝)网架(网片)芯板放入模腔,同样需有效定位,以保证浇注面层的厚度及芯板的位置,然后浇注面板。
3、面板、芯板先后成型可选择类:此类复合板可根据用户的条件、取向选择。
4、立模挤压式薄抹灰成型类:此为标准化生产线,长、宽及厚度可调,工厂化生产各类薄抹灰聚苯夹心保温板,抹灰厚度3-15mm,年产10——300万m2。这些产品可用于外墙外保温,外墙内保温,内隔墙板,也可直接作外墙保温挂板,与钢结构配套使用。当然,更可引入装饰行业,作室外防水装饰板。
(二)无轻骨料、大空心率、普通混凝土轻型条板
目前,国内墙板市场上如前所述,用量最大、占据主导地位的是轻质圆孔内隔墙板。选用轻质材料是为了降低面密度,抽孔也是为了降低面密度。至于选用圆孔是为了成型方便。
常用的轻骨料有膨胀珍珠岩、膨胀聚苯球、膨胀陶粒、蛭石及微珠、泡沫玻璃等。
不同的生产工艺如立模、平模、挤压机均可生产轻质圆孔墙板。
轻集料的加入,固然降低了面密度,但其负面影响接踵而来,大有得不偿失之感:一是轻集料的加入使得墙板干收缩值增大,直接导致板缝开裂的可能加大;二是轻集料的加入使水灰比加大,使得墙板强度降低;三是轻集料的加入,成本上升,导致利润下降;四是轻集料一般为高碳产品,不利环保,若碳税开征,又将进一步增加成本。
如何趋利避害呢?“无轻骨料、大空心率、普通混凝土轻型条板”是最好选择。
上述可知,传统“轻质”空心条板是以添加轻骨料来降低面密度,但同时也带来了强度低、干缩值大,成本上升,碳排放高等负面影响,而此“无轻骨料、大空心率、普通混凝土轻型条板”则是以提高空心率来降低面密度,以达到质轻、高强、低干缩、低成本、低碳排的目的。尽人皆知的道理是,普通混凝土最可靠,空气最便宜,节材低碳最环保。
其物理力学性能指标见表:
当然,这种条板的生产需要先进的装备来保证。
(三)石膏类条板的生产
成组立模的生产效率,抛开其自身的先进化程度,可操作性能暂不讨论,主要是由成型材料在模腔内的滞留时间来决定的。
石膏的快速凝固是成组立模最适宜的特性之一,而成组立模的模腔成型方式也是石膏这种大流动度料浆的不二选择。所以,从成型工艺的角度看,石膏与成组立模是一对绝配。
基于石膏的速凝特性,在选用成组立模成型工艺时,由于生产效率高,所以设备投资相比生产水泥基料墙板而言,要少的多,成组立模使用量仅为1/4——1/20。
但是,同样基于石膏的速凝和大流动度特性,其对生产装备的要求也比较高:
1、较高的效率:石膏的速凝特性决定了生产循环周期短、频率高,那么装备只有高度机械化、自动化,才能适应这种需要,并且要求整个工艺过程要完善、成熟,不能有“卡脖子”现象,以免影响整体效率。
2、有效的密封:石膏的大流动度使其对成组立模的密封性能要求相当苛刻,当今生产石膏条板的成组立模由于未寻找到有效的密封方式,大部分立模漏浆比较严重。采用“硬密封”效果较差,采用“软密封”寿命较短,这也是制约行业发展的技术瓶颈之一。
本世纪初,我们曾经花费了两年时间,专门对密封,包括密封形式、应用材料(密封材料及粘结材料)联接方式、使用寿命、工艺可行性、生产效率和生产成本等,进行了深入研究,大密度实验,但结果并不理想。当时我们戏称:举公司之全力,竭天下之密封材料,尽世界之密封胶,何其壮观,无果而终。当然,这也是创新的代价。今天,由于“不漏浆成组立模”产品的问世,此问题已得到圆满解决。
另外,石膏的微酸性特点,也决定了装备表面处理的重要性。石膏的微酸性使其对钢铁材料的腐蚀问题相当突出,如何对立模的不同部位进行不同方式的表面处理至关重要,因为这不但影响到设备的使用寿命,还关乎到所生产墙板的质量。更高级别的表面处理方案是:表面防腐与表面渗透、长效隔离综合考虑。
三、成组立模的发展经历了三个阶段:
第一阶段:上世纪五十年代中期,单组模腔的单体立模和双组模腔的“靠模”,由前苏联传入我国。其中双组模腔的“靠模”与单体立模相比,具有按放时的稳定性较好,操作方便等优点,故“靠模”得到了较为普遍的应用。所谓“靠模”是指两个单模背靠背的放置在一个公用的中隔板两侧,也即中隔板固定不动,两侧的两个侧板可向外侧开启。“靠模”操作简单,使用方便,便于维护,至今仍在一些小规模或复杂形状构件生产中应用。
第二阶段:是指单体立模或双体靠模的成组化发展。也即一台立模由原来的一组模腔、两组模腔发展为多组模腔。模腔数一般为八组、十组、十二组、十六组、二十组,至此,单体、双体立模完成了向成组立模的进化。宏观上看,从上世纪六十年代中期开始,直至九十年代中期,三十多年来,成组立模在国外如前苏联、匈牙利、朝鲜,在国内如北京、上海、广东、东北等地,都有了丰富多彩的发展。
运用“奥卡姆剃刀”,剔除枝枝节节,仅从主体结构形式看,成组立模的种类有半拆装式立模,全拆装式立模,悬挂式立模,传送带立模,芯模固定、外模移动式立模,柔性隔板立模等。其中,全拆装式成组立模的应用较为广泛。
以十六组模腔的全拆装式成组立模为例,它主要有底模、侧模隔板、端模堵板三个部分组成。
1、底模:底模可以是一个带底座的钢底模,也可以是水泥平台,侧模隔板和端模堵板安装置于其上。
2、侧模隔板:十七块侧模隔板水平侧立在底模上,组成十六个模腔,模腔间隔即墙板厚度。
3、端模堵板:三十二块端模堵板置于十六个模腔的两端,并被侧模隔板夹持定位在给定的位置上。
组装定位、施力夹紧后,即可进行浇注。当养护达到一定强度后,便可松开夹紧装置,拆掉侧模、端模,取出墙板,之后,进行第二个循环。当然,模腔内可以布网,端模堵板可以是带孔的,以便穿入芯管,形成多孔墙板。
另外,与传统立模安装方式不同的一种竖置立模即竖模,也于九十年代中期在广东出现。传统立模大都采用“侧立”,也即宽度方向立起的安装形式,而竖模则是采用“竖立”,即沿长度方向立起的安装形式。
立模与竖模的主要组成部件基本相同,区别在于其部件的安装形式不同,料浆的浇注特点不同。
立模与竖模的主要组成部件基本相同,区别在于其部件的安装形式不同,料浆的浇注特点不同。
立模是隔板侧立安装,芯管水平布置,浇注高度只有600mm,所以,有利于浇注。但水平布置的芯管对料浆向下流动形成一定的阻力。
而竖模则是隔板竖立安装,芯管垂直布置,浇注高度可达3000mm以上,所以料浆行程较长,不利于浇注。但垂直布置的芯管对料浆向下流动阻力较小。
成组立模与单模、“靠模”相比,生产效率要高得多,具备了工厂化生产的条件。
第三阶段:进入了“机械动力成组立模”时代。第二阶段多种多样的成组立模均属手工开合模、手工组拼式立模,均属工具式模板的范畴。而“机械动力成组立模”(简称机动成组立模)则是开启了成组立模的一个新时代。至此,成组立模进入了机械装备行业,也即成组立模由工具式模板升华为机械装备,完成了其由马车向汽车的飞跃,为成组立模墙板生产的机械化、自动化、标准化、规模化、产业化奠定了基础,也为成组立模主体工艺技术与当代其它领域的先进技术进行模块化拼接、多种技术集合、成熟技术集成打造了一个应用平台。